Smart factory
Smart Factory – The digitalized production
Using digital tools does not necessarily make a production "smart". Digital solutions enable the smart factory to be characterized by a high level of transparency and proactive identification of deviations in the production process based on intelligent data analysis.
The basis of process visualization and anomaly detection is the acquisition of relevant data on the shop floor and its transfer to higher-level systems for evaluation and visualization. In the end, the efficient processing of production data is key to enable well-founded decision-making at an early stage.
As part of the Dürr Group we have vast experience in planning and implementing digital solutions in production. Established OEMs in the automotive sector are among our customers, as well as e-mobility start-ups and companies with discrete manufacturing in the general industry.
Connected and digitalized production equipment is a core precondition for the smart factory. To get there efficiently, we support you from initial planning to implementation. For the planning phase, we offer our customers the following services in accordance with the ISA-95 automation pyramid.
MES consulting - planning of the manufacturing execution system
On the path to the Smart Factory
As the central hub for production data, the MES system provides the basis for the smart factory. The consolidation and analysis of production data in a plant-wide system enables industrial companies to increase planning accuracy, enhance process and product quality, improve equipment availability and achieve near-real-time process transparency.
A decisive factor for IT-supported production control and monitoring is the close interlocking of process planning, equipment planning and production IT planning. The necessary functional requirements for the SCADA (Supervisory Control and Data Acquisition) and the manufacturing execution system (MES) can only be derived from the specific process requirements. Thus, the consideration of process- and customer-specific requirements always provides the basis for the functional design of the systems in our concept planning.
Once the functional requirements have been described in MES Use Cases, we work with our customers to determine the non-functional requirements. They are divided into technical requirements, such as requirements for fail-safety, and non-technical requirements, such as the provision of training and hotline support. The non-functional requirements are influenced by the functional requirements as well as by the internal IT guidelines of our customers and common industry standards.
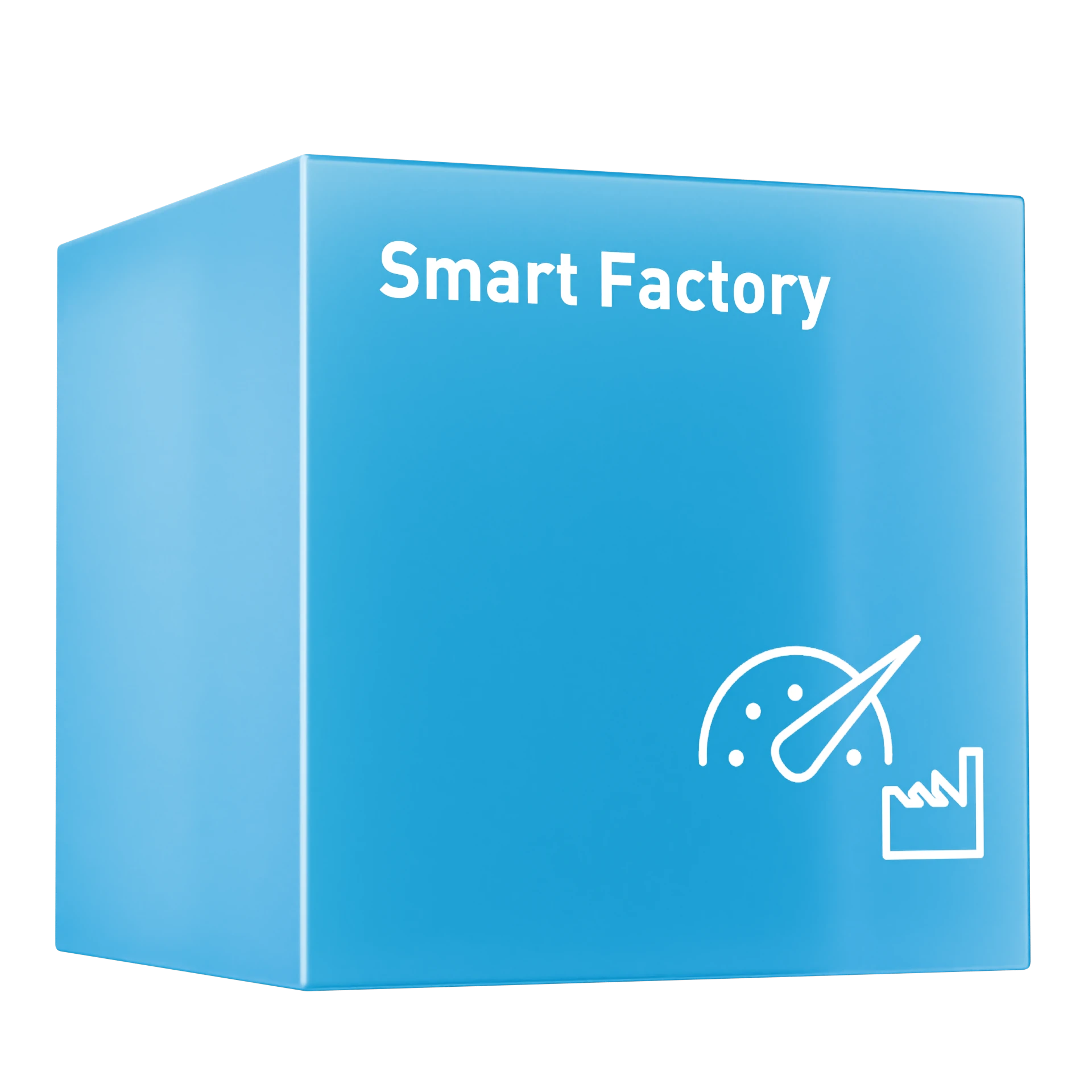
Always keeping the interfaces and flow of information in mind
In the modern world of production IT, functions such as maintenance and warehouse management are supported by different systems, depending on the company. Maintenance tasks, for example, can be managed in the ERP system, the MES system or a dedicated maintenance assistant. It is therefore necessary to always take the customer's existing IT infrastructure into consideration rather than believing in one-fits-all standard solutions.
From this perspective, it is also necessary to consider the interfaces to other IT systems such as ERP, PLM, warehouse management or even specialized systems for detailed planning or quality management. By positioning the individual functions in the entire system landscape, the necessary information flows between the systems can then be determined.
SCADA system – the interface to the field level
While the MES level focuses on the consolidation and processing of various data, it is usually the SCADA level that provides the physical interface to the shop floor. As part of the SCADA planning, the interfaces to the field level, including the relevant communication protocols, are defined. This is done in close coordination with the responsible planners of the control concept and the equipment planners.
Control concept planning
At level 1 of the automation pyramid, the so-called control level, Dürr Consulting offers the planning of the control technology concept. Together with the responsible planners for equipment and production IT, general control standards are developed that enable flexible, automated, and digitalized production. In addition, the early harmonization and integration of individual stations or machines from a wide variety of suppliers into the IT/OT system landscape is ensured. During the development of the control technology concept, we support you, among others, in the following aspects:
- Design of the control architecture:
- Specification of the topology (line or station PLC, IO devices, etc.)
- Network design
- Connection to MES/ERP systems
- Definition of standards for hardware design:
- Selection and specification of standard components (e.g. IO devices)
- Specifications for naming and linking signals (E-PLAN)
- Specifications for networks (topology, components)
- Definition of standards in software development (PLC):
- Selection/specification of engineering systems and programming languages
- Modularization of software
- Definition of interfaces and data structures
- Specification of interfaces between MES and PLC level
- Virtual commissioning and simulation
- Development of a visualization/operating concept
Production equipment planning
As part of the production equipment planning, Dürr Consulting addresses the requirements of the bottom level of the automation pyramid, the field level. In accordance with the requirements set by the control technology concept and the superior control systems, the sensors and connectivity on machine level is defined. The components relevant to the processes are selected and their integration into the equipment technology is ensured by selecting and specifying standardized interfaces and protocols.
Digital Use Case planning
Often the focus is not on factory-wide production IT systems, but rather on technological solutions for specific challenges. For example, how a track and trace solution can be retrofitted in a brownfield factory. If the relevant technologies are based on operation technology or production IT technology, we refer to this service as digital use case planning.
The scope of these digital use cases is diverse and has recently comprised the design of an operator guidance system, the specification of traceability systems, the conceptual design of failover redundancy for production-critical IT systems, as well as a state-of-the-art Andon system, which combines the principles of lean management with the advantages of modern digital solutions.
During the concept planning we join forces with leading suppliers and their technology experts to ensure that the designed solutions are both, based on state-of-the-art and yet reliable technology.
Digital Readiness Assessment
Learn how Dürr Consulting can help you develop a structured digitalization roadmap by assessing and developing the current status and vision for your business
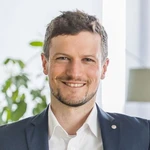
Carl-Benz-Str. 34
74321 Bietigheim-Bissingen
Germany