Consulting drives new state-of-the-art battery assembly
Starting with an almost blank slate and ending with a run up to full capacity battery pack assembly in the specified time and quality, that was the job of Dürr Consulting in consultancy and planning support for a premium car manufacturer. This was one of the main challenges along with the definition of new standards which are matched to the existing production system and the low product maturity due to late product development. This case study demonstrates that an excellent methodical and systematic approach develops a state-of-the-art battery assembly that meets the customer requirements in quality, time and cost.
Approach
The above figure shows the specific Dürr Consulting project approach based on methods, tools and a strict focus on earnings. With this approach, Dürr Consulting is defining the project targets with KPI’s to measure the fulfillment at the end of the project. All project phases are treated as sub-projects, that means each has its specific targets and KPI’s. At the end of each phase a partial approval, in combination with milestone-specific Q-gates is completed. The roadmap for the next phase in relation to the actual status of the overall goal is to be reviewed and realigned to guarantee the project’s success at any time. This approach is to be aligned and defined in the project kick-off with the OEM client.
Project targets
Current targets for a state-of-the-art battery production plant for premium battery vehicles (BEV):
- State-of-the-art assembly for battery pack 75/95 kWh for EV, 3 different types
- 20 jph, 2-shift assembly, 300 units/day, total production volume 500,000 units/lifecycle
- 95 % availability, decoupling of line segments
- Assembly close to point of use by integration in existing building (Brownfield)
- Comply with fixed area in existing building
- Productions type: component assembly without sequence to final assembly
- Battery modules from different suppliers with different cell types and cell connections
- Highly efficient assembly process with consideration of high-voltage safety measures
- Automation of processes due to high voltage, high weight handling and quality requirements
- Define standard process, layout and equipment for battery pack assembly
- Flexibility in output and capacity increase
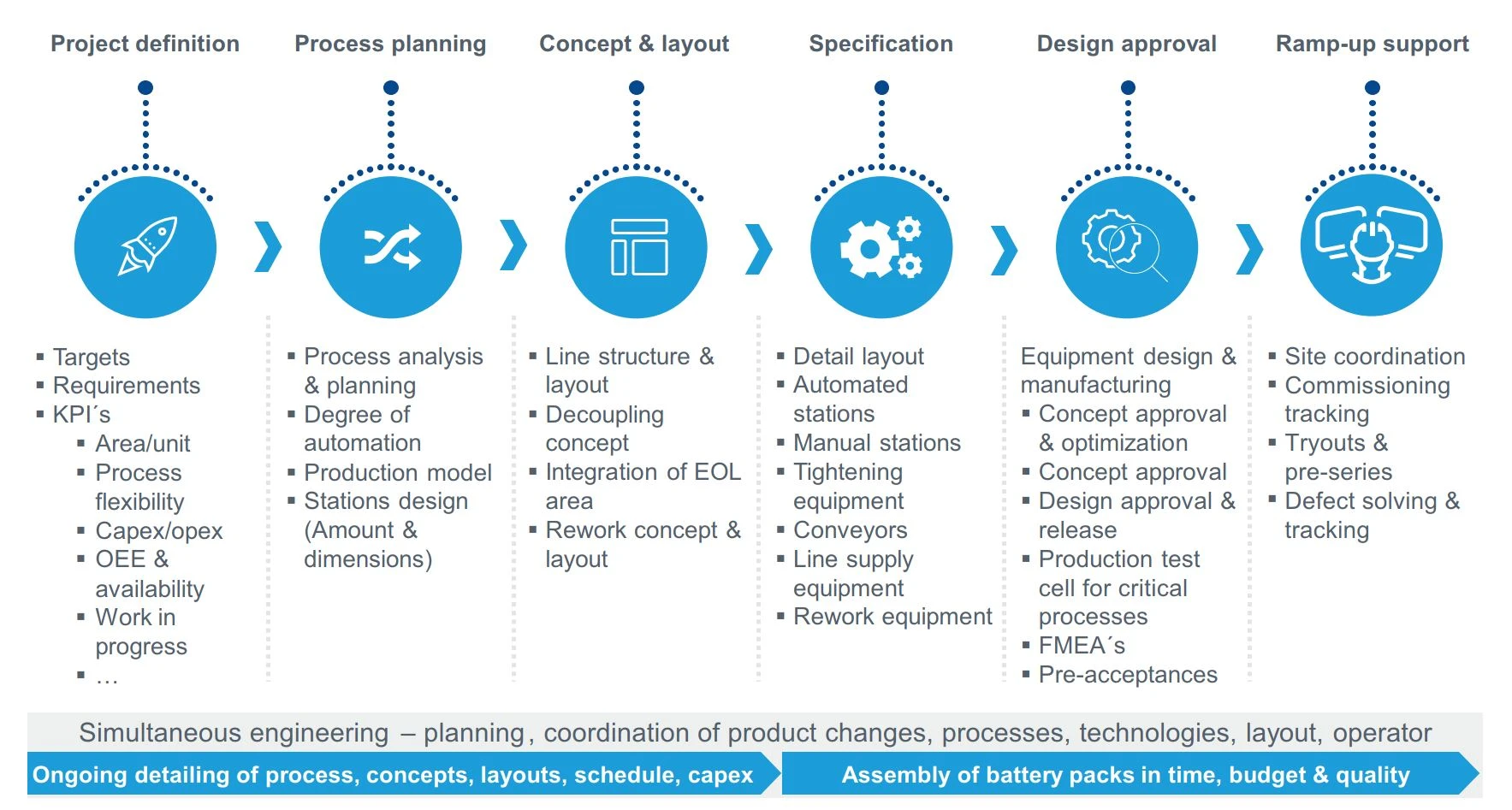
Main project challenges
Assembly time: At the start of the project, the focus is to define the process and content of automation to build up the needed assembly time. Since mass production of battery packs for BEV is a relatively new demand for established OEMs, the specific standards, technologies, processes and production times need to be reviewed and adapted to the new processes and technologies. Therefore, it was very important to estimate and generate a realistic assembly process and realistic times for the entire assembly and testing including:
- Definition and dimensioning of space, flow, station design & amount, decoupling
- Developing and selection of needed technology, especially for high voltage
- Evaluation and definition of degree of automation
Product maturity: Many changes to the product force ongoing revision of the processes, technologies and sequence without increasing the timeline and space requirements on the one hand. On the other hand, this offers the opportunity for integration of product features (e.g. reference holes), which enables optimization of the processes and higher production quality.
Supply of space: The challenge here was to fit the battery pack assembly into a given foot print. To maximize space for assembly lines and equipment, necessary functions such as line-to- line transfers, decoupling and buffering, control cabinets, cleaning devices/stations, maintenance and office space need to be evaluated and alternative solutions for space optimization, e.g. platforms or second floor level, need to be found.
Further challenges
In addition, the following challenges have to be met by optimizing and developing procedures:
- High joint accuracy for fitting modules versus achievable tolerances at battery tray and production cost
- Electrical codes and new requirements for assembly under high voltage should not result in additional processing times and tests or limit the overall effectiveness
- Preliminary approvals only with pre-series parts that do not have the final series design
Project success factors and highlights
Cooperation with Dürr Consulting enables the OEM client to design, install and ramp-up a state of the art battery pack assembly.
- Simultaneous engineering and design for manufacturing in close cooperation with product development, production planning and operating division
- Stringent project and interface management ensures timely and high-quality realization within project budget
- Prompt process, equipment and system approvals by strict action tracking
- High team spirit: high engagement and commitment to “go the extra mile”
- Benchmark concept to be applied for future battery assembly projects
Outlook: OEE optimization through digital applications
Scalable and flexible battery assemblies with increasing product variants require digital applications which improve the OEE and stabilize manufacturing processes. Dürr Consulting is able to provide consulting, directional determination and implementation of digital solutions for battery assemblies. Thus, we ensure equipment availability and product quality at the same time. Our Digital Readiness Assessment for the shop floor delivers an actual reflection of your digital readiness within 3 days and enables the discussion of measures for additional efficiency increase in your production.