Smart concept for flexible hydraulic motor assembly
In a recent interview an automotive expert affirms: “If someone asks for lean vs. smart I’ll tell him that we definitely need a combination of both.” Not only in the automotive industry, but in all industries, a lean, smart and flexible production is the key to success in today’s fast-moving and demanding market. In this context, Dürr Consulting was asked by a world-leading manufacturer of hydraulic motors to develop the vision and concept of a future-ready, flexible and adaptable assembly line in 4 months only.
Project challenges & Approach
In the current production, different challenges like high product variance, unbalanced process-to-station-assignment and buffers, critical ergonomics, asynchronous line supply and unreliability of testing equipment cause a lack of quality and delayed deliveries. To understand all challenges and define targets for the future line, the first step was the collection of basic data and a detailed process analysis. This was the basis for the creation of innovative equipment concepts, logistics supply modes and a future line structure.
Detail analysis and digital twinning
The most effective method of process analysis is to record the actual process and findings during production on site. Thus, all problems within the current process and equipment can be observed and documented transparently. By assigning MTM time-units to all handling steps, the process is described in a very detailed manner. That allows movements to be classified into value-adding and inefficient handling step.
The entire process, equipment and manual labor forms the basis of a comprehensive 3D simulation model, which is represented as a digital twin. With the model of the existing production line ergonomics, distances and line balancing can be evaluated. In addition, process changes can be tested by measuring varied, relevant parameters in the model.
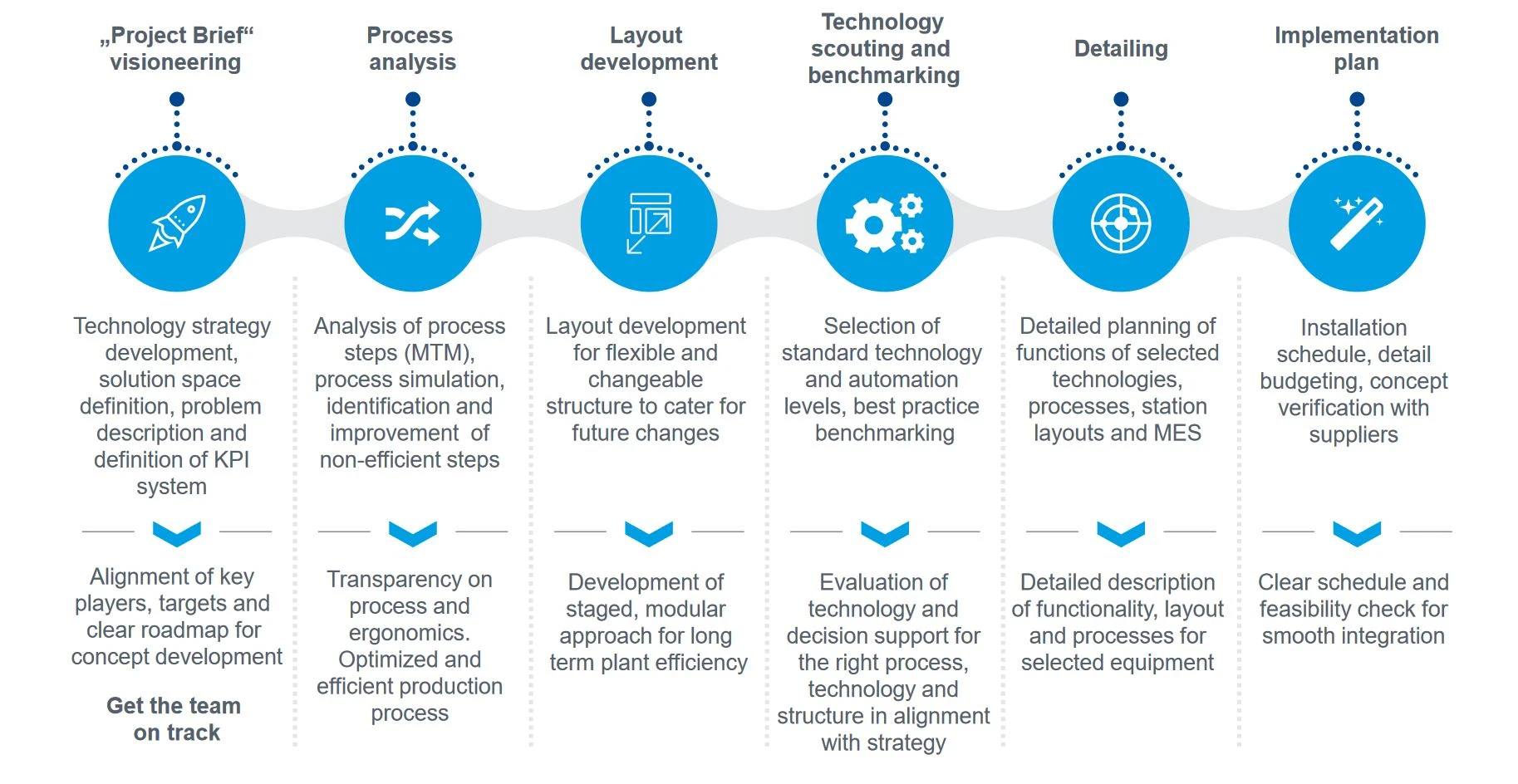
Designing a smart production concept
Based on the results of the analysis, it was possible to define targets and KPIs for the future line in workshops with all departments involved:
The main target was to streamline the production by optimizing the material flow with reduced work in progress and buffers, an adapted and balanced process-to-station assignment and a smart extension strategy. To meet those targets the digitalization of production, process and logistics control has been identified as one key lever. A second set of targets was to improve quality and ergonomics which was achieved by innovative and reliable process and testing equipment as well as visual poka-yoke systems.
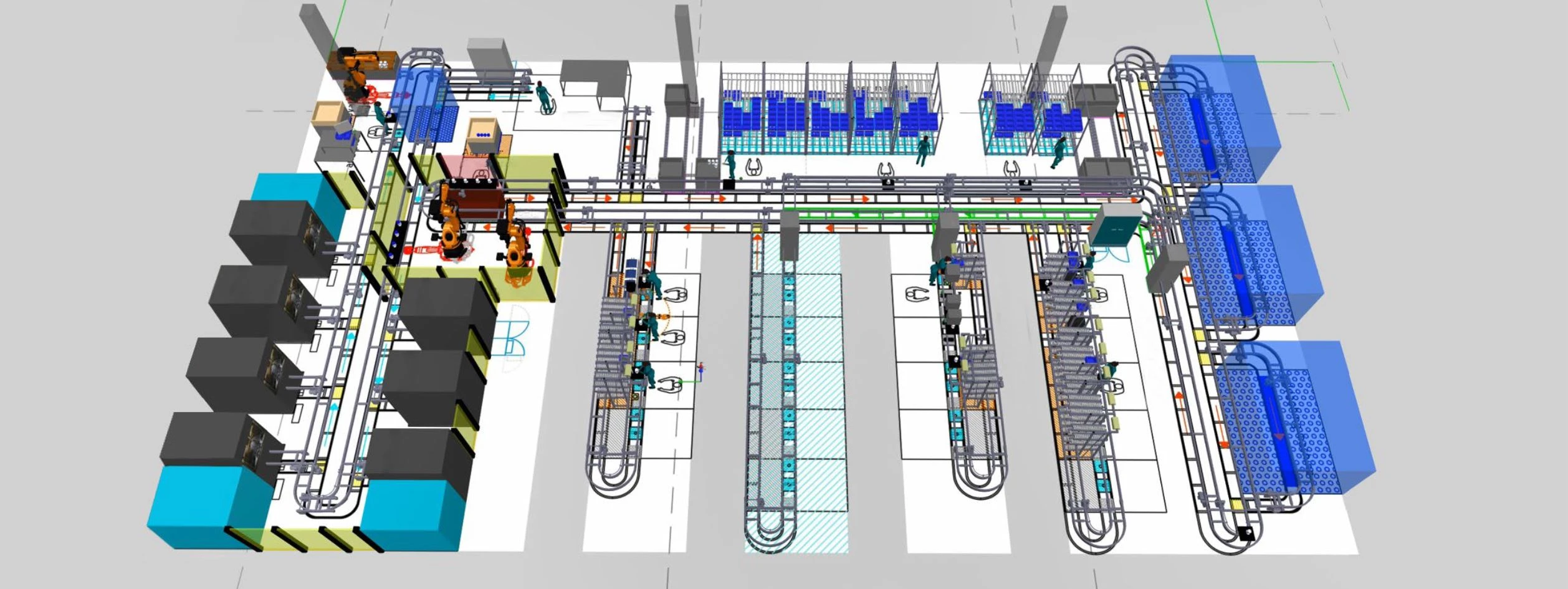
Those targets make clear that the current line arrangement, station balancing, and equipment had to be completely re-evaluated. Station calculation and line balancing were done using the times of the MTM-analysis minus inefficient handling times. The outcomes from the analysis and simulation showed that the line needs to be arranged in a matrix structure connected with conventional conveyors in order to allow for the high variance of products while still maintaining the high required output volumes. The analysis showed that some process steps have to be shifted to product-specific subassemblies while the final assembly is done in only four common main assembly stations, followed by a fully automated testing area. Thereby changeover times are eliminated so that even a one-piece flow is possible. For each process, different technology options and levels of automation were evaluated. The most efficient equipment was selected regarding cost, flexibility and fit with the technology strategy. To evaluate efficiency, a second simulation has been performed (see fig. 2). In this way it could be proven, that all preselected KPI targets aligned in customer workshops can be achieved in future production.
Customer Benefits
- Fully flexible production concept: The new concept allows for a completely flexible, changeable and scalable assembly of six totally different products in one line – with optimum worker and equipment utilization. By implementing a kitting zone and optimized station layouts, inefficient handling steps were eliminated, and ergonomics improved.
- Clear roadmap and strategy for future production: Based on the customer’s current drivers and overall strategy a clear roadmap for technology integration has been derived. For different volume and economic scenarios standard equipment has been defined to guarantee efficiency, quality and availability.
- Future-readiness and digitization: Using the specified MES system, logistics processes can be designed more flexibly and stock of material is reduced. In addition, smart product tracking and automatic production planning prevents delayed deliveries to customers. Smart tools guarantee quality parameters and worker guidance supports operator training required due to high fluctuation.
In summary, lack of production control, complex line balancing, inefficient handling, inflexible equipment and the lack of production tracking restricted efficiency in the old production line. For the new concept those issues were eliminated by a new structure and modern equipment and clear roadmap – the production line is now ready for the future.