Entwicklung eines maßgeschneiderten MES-Konzepts
Ein Manufacturing Execution System (MES) unterstützt Fertigungsunternehmen bei der Erhöhung der Planungsgenauigkeit, der Prozess- und Produktqualität, der Anlagenverfügbarkeit und der allgemeinen Prozesstransparenz. Darüber hinaus ist das MES als zentrale Drehscheibe für Fertigungsdaten die Basis für die Smart Factory. Insbesondere die Automobilindustrie setzt bereits seit Jahren auf eine IT-gestützte Produktionssteuerung und -überwachung. Diesem Trend folgen zunehmend auch andere Branchen, wie dieses Fallbeispiel eines Landmaschinenherstellers zeigt. Im Rahmen eines Masterplanungsprojekts hat das Unternehmen Dürr Consulting beauftragt, ein auf die spezifische Situation und Vision des Kunden zugeschnittenes MES-Konzept zu entwickeln.
Herausforderungen und Ansatz des Projekts
Der Kunde hat die Vision formuliert, ein neues Produktionskonzept zu entwickeln, das die effiziente und flexible Herstellung von hochwertigen Produkten ermöglicht. Aufgrund wiederkehrender Qualitätsprobleme und eines Mangels an umfassender Produktverfolgung und -dokumentation forderte die Geschäftsleitung ein MES-Konzept zur Steuerung und Überwachung des neuen Produktionssystems. Das Konzept eines MES war für den Kunden jedoch neu, da er bisher kein solches System im Einsatz hatte. Daraus ergab sich die Herausforderung, bei der Konzeptentwicklung mit wenig vorhandenem MES-Wissen und -Erfahrung auf Seiten des Kunden umzugehen. Ähnlich wie bei der Entwicklung des Layouts und der Konzeptplanung für einzelne Shops (z.B. Lackierung) folgte die MES-Konzeptplanung einem dreistufigen Ansatz, bestehend aus einer Phase der Bestandsaufnahme, einer Konzeptplanungsphase und einer Detailplanungsphase.
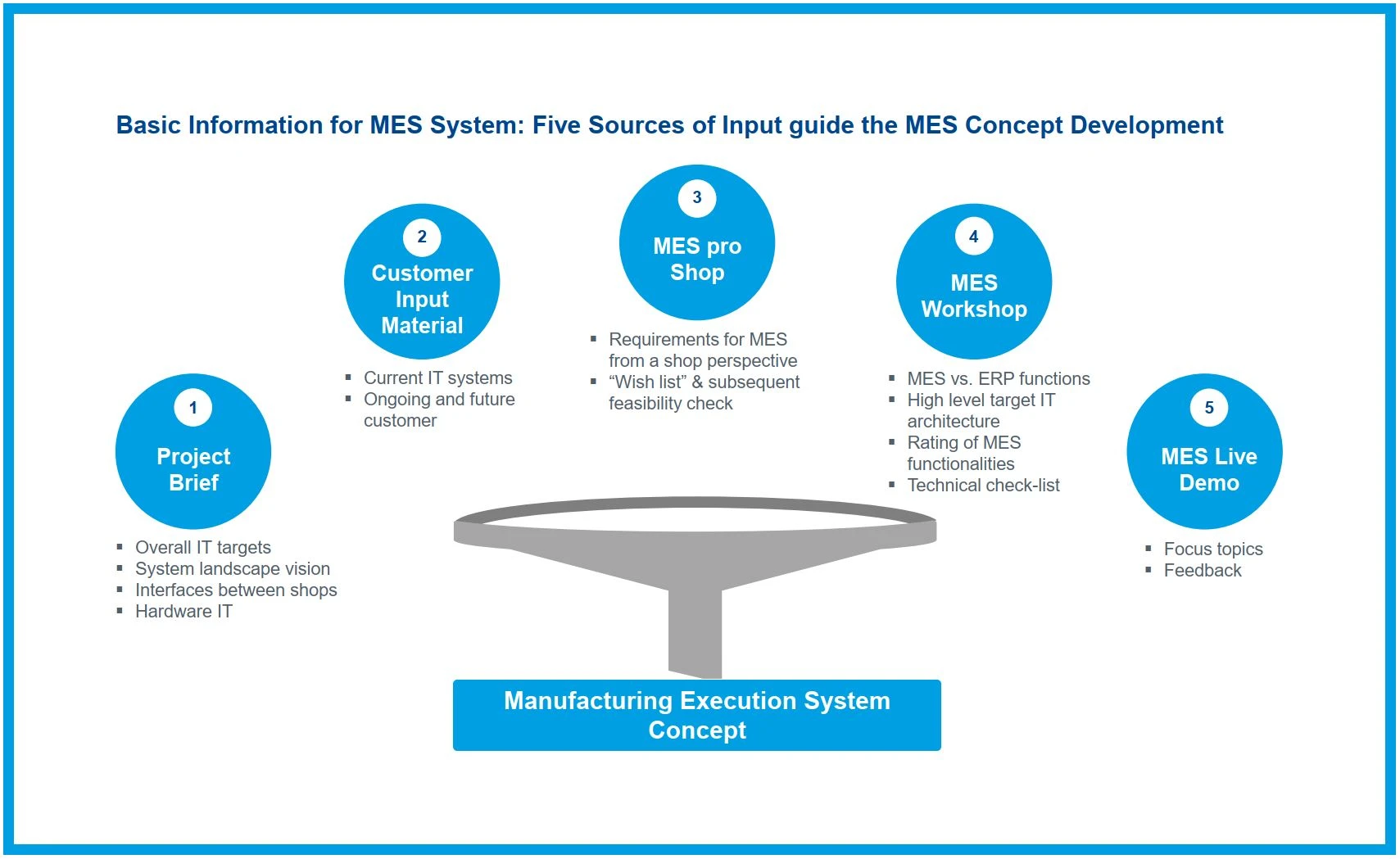
Bewertung des Status quo
Die Ziele des Kunden bezüglich der IT-Systeme wurden als Grundlage für die Konzeptentwicklung vereinbart. Um sicherzustellen, dass das neue MES-Konzept in die bestehende IT-Infrastruktur passt, hat das Projektteam Dokumente der bestehenden IT-Landschaft gesichtet. Da die IT-Infrastruktur in der Regel ständigen Anpassungen unterliegt, wurde auch die geplante Einführung von IT-Systemen diskutiert. Dabei stellte sich heraus, dass der Kunde bereits mehrere ERP-Add-ons im Einsatz hatte, die zum Teil die Funktionalität eines MES-Systems abdecken.
Die obige Abbildung gibt einen Überblick über die fünf Informationsquellen, die in der Konzeptplanungsphase als Grundlage für die spätere Entwicklung des MES-Konzepts herangezogen wurden.
Konzeptplanung - von einem allgemeinen mes zu einem kundenspezifischen mes-Konzept
Um das Verständnis des Kunden für MES-Systeme zu verbessern und eine gemeinsame Basis für weitere Diskussionen zu schaffen, wurden standardisierte und herstellerunabhängige MES-Funktionalitäten auf Basis der renommierten VDI-Norm 5600 vorgestellt und mit dem Kunden diskutiert.
Auf der Grundlage des Überblicks über die MES-Funktionalität und des Inputs des Kunden wurde ein gemeinsamer MES-Workshop organisiert. Da einige Funktionen (z.B. Auftragsmanagement) entweder im ERP- oder im MES-System realisiert werden können, war das erste Ziel des Workshops zu klären, ob das ERP- oder MES-System für eine bestimmte Funktion besser geeignet ist. Das zweite Ziel war es, Standard-MES-Funktionen hinsichtlich ihrer Relevanz für den Kunden zu bewerten - entweder obligatorisch, gewünscht oder optional.
Nach einer Bestandsaufnahme der aktuellen IT-Landschaft und der Anforderungen des Kunden an die werksweiten MES-Funktionalitäten ging das Dürr-Team in die Detaildiskussion. Unter dem Motto MES pro shop überprüften die mit der Planung eines neuen Konzepts für die Lackiererei, die Logistik, die Schweißerei, die Montage und die Prüferei betrauten Teammitglieder den geplanten Prozess, um Möglichkeiten für Prozessverbesserungen durch MES-Systemunterstützung zu identifizieren. Die daraus resultierende Wunschliste wurde dann von internen MES-Experten auf die Realisierbarkeit der formulierten Anwendungsfälle hin bewertet. Basierend auf dem Input der Shop-Planer wurde pro Shop ein One-Pager erstellt, der die relevanten Use Cases (z.B. Werkerführung) zusammen mit der benötigten Hardware (z.B. stationäre und mobile MES-Clients und Barcodescanner) und dem Informationsfluss (z.B. (1) vom Barcodescanner zum MES, (2) vom MES-Backend zum MES-Client und (3) vom MES-Client zurück zum MES-Backend) beschreibt. Schließlich wurden alle in den verschiedenen Geschäften geplanten MES-Anwendungsfälle konsolidiert und in einer Präsentation detailliert erläutert.
Um die etwas abstrakten MES-Funktionen greifbarer zu machen und dem Kunden das Look & Feel eines hochmodernen MES-Systems zu vermitteln, wurden MES-Live-Demos durchgeführt. Die Demo wurde als eine Kombination aus der Präsentation von vorbereiteten Anwendungsfällen und Ad-hoc-Demonstrationen von Kundenwünschen organisiert. Die Live-Demo erwies sich als effektiv, um detaillierte Diskussionen über bestimmte, kundenspezifische Anforderungen zu unterstützen. Darüber hinaus ermöglichte sie eine erste Einschätzung, ob die Anforderungen des Kunden bereits durch eine Standard-MES-Lösung abgedeckt werden können oder ob individuelle Entwicklungen notwendig sind. Wurden für einen Anwendungsfall (z.B. Materialnachschub in der Fertigung) verschiedene Lösungen vorgestellt, wurde das Kundenfeedback aufgenommen und als weiterer Input für das kundenspezifische MES-Konzept berücksichtigt.
Schließlich wurden - unter Berücksichtigung aller Beiträge (siehe Abbildung 1) - drei MES-Konzepte entwickelt und vorgestellt (siehe Abbildung 2). Jedes Konzept wurde nach bestimmten Leitprinzipien entworfen. Konzept 1 mit dem Titel "Basic MES" verfolgte einen minimalistischen Ansatz und konzentrierte sich auf die Integration nur wesentlicher Funktionen, um CAPEX und OPEX auf ein Minimum zu beschränken. Der Leitgedanke von Konzept 2 "Advanced MES" bestand darin, alle obligatorischen Anforderungen des Kunden und die Forderung nach einer umfassenden Anwendung von Mitarbeiterführungsclients in der neuen Fabrik zu erfüllen. Konzept 3 stand unter der Maxime, das volle Potenzial moderner MES-Systeme auszuschöpfen und umfasste im Gegensatz zu Konzept 2 auch zusätzliche Funktionen wie FTS-Steuerung, Fertigungsanalytik und Energieüberwachung. Darüber hinaus schlägt es den flächendeckenden Einsatz von mobilen Werkerführungssystemen zusätzlich zu den stationären vor. Die drei Konzepte sind in einem One-Pager zusammengefasst (siehe Abbildung 2), in dem die Gestaltungsprinzipien des Konzepts sowie die Vor- und Nachteile eines Konzepts aufgeführt sind. Darüber hinaus gibt Dürr eine Empfehlung für ein Konzept ab und begründet diese Empfehlung. Um den Kunden bei der Auswahl zu unterstützen, wird für jedes der drei Konzepte eine Budgetangabe gemacht. Die Angabe umfasst die CAPEX für Softwarelizenzen, Servicekosten für die Implementierung und Hardwarekosten sowie OPEX für Wartung und Support. Auf Wunsch des Kunden können die vorgeschlagenen Konzepte aktualisiert werden, z. B. durch Hinzufügen einer Funktion zu Konzept 2, die ursprünglich nur in Konzept 3 verfügbar war.
Kundenvorteile auf einen Blick
- Der vorgestellte Ansatz gewährleistet mehrere Kundenvorteile
- Überblick und Einführung in die Funktionalitäten moderner MES-Systeme
- Herstellerunabhängige Beratung auf der Grundlage etablierter Industriestandards und -normen
- Look and Feel von MES-Systemen durch Live-Demonstration
- Drei Konzepte mit klarem Leitbild und Vor- und Nachteilen
- Begründete Empfehlung
- Zeitplan und Budgetangabe
- Auf den Kunden zugeschnittenes RFQ-Dokument
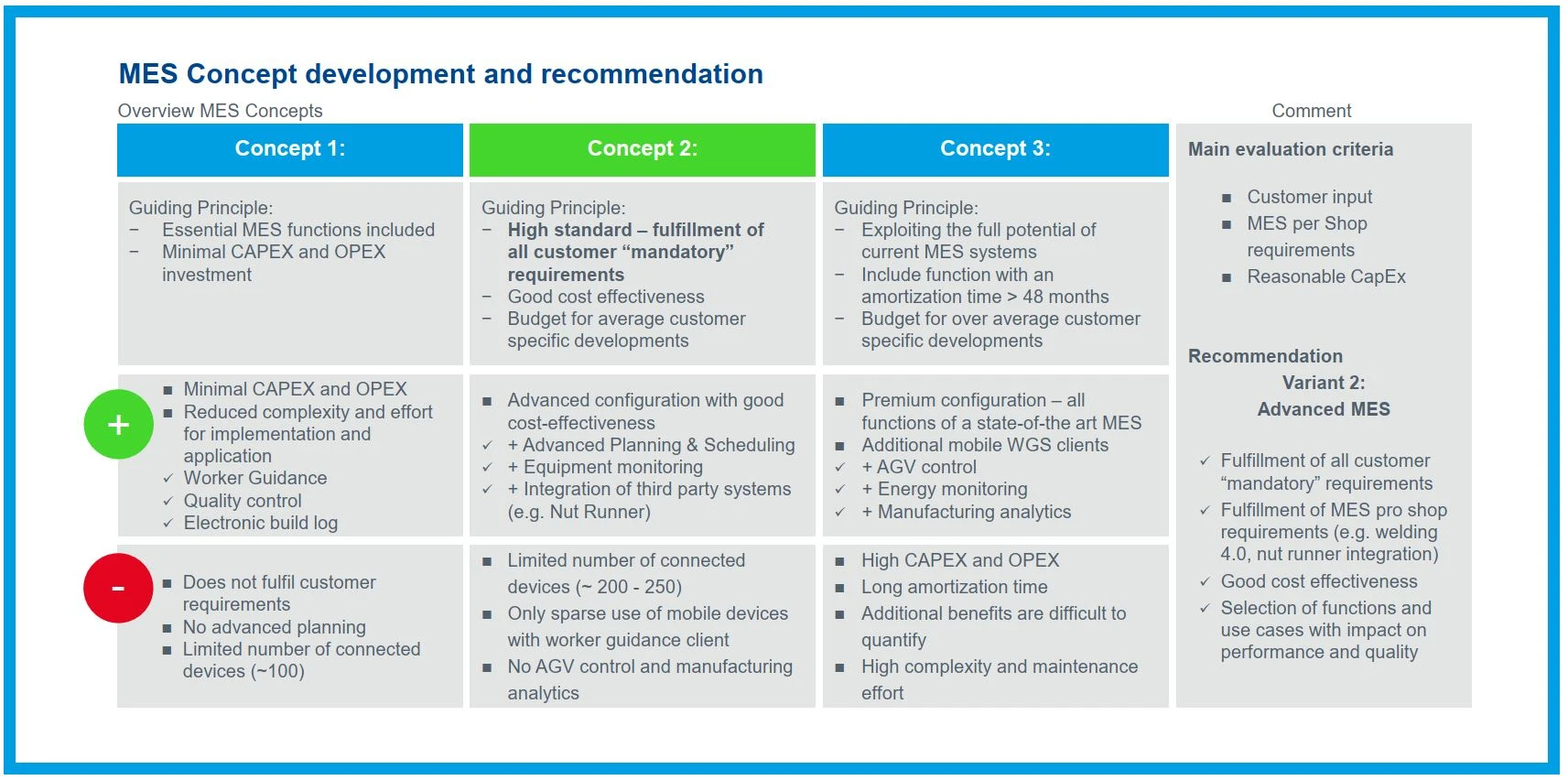
Detailplanung
Sobald sich der Kunde für ein Konzept entschieden hat, beginnt die Phase der Detailplanung. In dieser Phase wird das Konzept weiter detailliert. In enger Zusammenarbeit mit internen MES-Experten und auf der Grundlage bereits realisierter MES-Projekte wird ein Projektzeitplan erstellt, der die wesentlichen Implementierungsphasen umfasst. Der Zeitplan ermöglicht es dem Kunden, einen geeigneten Zeitpunkt für die Einholung von Angeboten von MES-Anbietern zu wählen, der die Auswahl und Implementierung des neuen Systems ermöglicht, so dass es zum geplanten SOP fertig ist. Basierend auf dem aktuellen Planungsstand der einzelnen Shops und den geplanten MES-Anwendungsfällen pro Shop wird eine Liste der benötigten Hardware erstellt. Diese Liste umfasst in der Regel die folgenden Hardwarekomponenten: Server, Desktop-Rechner, fest installierte und mobile MES-Clients, Andon-Boards, Scanner und Drucker. Durch die Konsolidierung aller Hardware-Anforderungen des MES-Systems über alle Shops hinweg wird dem Kunden neben dem Konzept auch eine detaillierte Ausstattungs- und Budgetliste zur Verfügung gestellt.
Dokumente für die Angebotsanforderung
Der letzte Schritt in der Detailphase ist die Erstellung des Ausschreibungsdokuments (RFQ). Das gemeinsam verabschiedete MES-Konzept bildet die Grundlage für das Anfragedokument. So wird sichergestellt, dass die Anbieter geeignete Lösungen für den kundenspezifischen Kontext und die Anforderungen vorschlagen können. Das Ausschreibungsdokument für MES-Systeme besteht aus drei Hauptkapiteln. Das erste Kapitel, Lieferumfang, beschreibt den Umfang der angeforderten Dienstleistung und Software und liefert einige Kontextinformationen über die Situation, Ziele und Erwartungen des Kunden. Das zweite Kapitel, funktionale Anforderungen, umfasst einerseits allgemeine, werksweit anwendbare funktionale Anforderungen wie Alarm, Track & Trace und KPI & Trends und andererseits werkstattspezifische Anforderungen wie die Überwachung der Prozessparameter in der Lackiererei. Das dritte Kapitel beschreibt alle nicht-funktionalen Anforderungen. Dazu gehören sowohl technische Anforderungen wie Verfügbarkeit und Genauigkeit als auch nicht-technische Anforderungen wie Customizing, Schulung, Dokumentation, Wartung und Support.