Beratung treibt neue hochmoderne Batteriemontage voran
Von einem nahezu unbeschriebenen Blatt bis zum Hochlauf der Batteriepack-Montage in der vorgegebenen Zeit und Qualität - das war die Aufgabe von Dürr Consulting bei der Beratung und Planungsunterstützung eines Premium-Automobilherstellers. Dies war eine der Hauptherausforderungen neben der Definition neuer, auf das bestehende Produktionssystem abgestimmter Standards und der geringen Produktreife aufgrund der späten Produktentwicklung. Diese Fallstudie zeigt, dass durch ein exzellentes methodisches und systematisches Vorgehen eine hochmoderne Batteriemontage entsteht, die den Kundenanforderungen in Qualität, Zeit und Kosten entspricht.
Näherung
Die obige Abbildung zeigt den spezifischen Projektansatz von Dürr Consulting, der auf Methoden, Werkzeugen und einer strikten Ergebnisorientierung basiert. Mit diesem Ansatz definiert Dürr Consulting die Projektziele mit KPI's, um die Erfüllung am Ende des Projekts zu messen. Alle Projektphasen werden als Teilprojekte behandelt, d.h. jede hat ihre spezifischen Ziele und KPI's. Am Ende jeder Phase wird eine Teilabnahme in Kombination mit meilensteinspezifischen Q-Gates durchgeführt. Der Fahrplan für die nächste Phase ist in Bezug auf den aktuellen Stand des Gesamtziels zu überprüfen und neu auszurichten, um den Projekterfolg jederzeit zu gewährleisten. Diese Vorgehensweise ist im Projekt-Kick-off mit dem OEM-Kunden abzustimmen und zu definieren.
Projektziele
Aktuelle Ziele für eine hochmoderne Batterieproduktionsanlage für Premium-Batteriefahrzeuge (BEV):
- Hochmoderne Montage für Batteriepacks 75/95 kWh für EV, 3 verschiedene Typen
- 20 jph, 2-Schicht-Montage, 300 Einheiten/Tag, Gesamtproduktionsvolumen 500.000 Einheiten/Lebenszyklus
- 95 % Verfügbarkeit, Entkopplung der Liniensegmente
- Montage nahe am Verwendungsort durch Integration in bestehendes Gebäude (Brownfield)
- Einhaltung der festgelegten Fläche im bestehenden Gebäude
- Produktionsart: Komponentenmontage ohne Sequenz zur Endmontage
- Batteriemodule von verschiedenen Lieferanten mit unterschiedlichen Zelltypen und Zellanschlüssen
- Hocheffizienter Montageprozess unter Berücksichtigung von Hochspannungssicherheitsmaßnahmen
- Automatisierung der Prozesse aufgrund von Hochspannung, hohem Gewichtshandling und Qualitätsanforderungen
- Definition von Standardprozess, -layout und -ausrüstung für die Batteriepackmontage
- Flexibilität bei Ausstoß und Kapazitätserhöhung
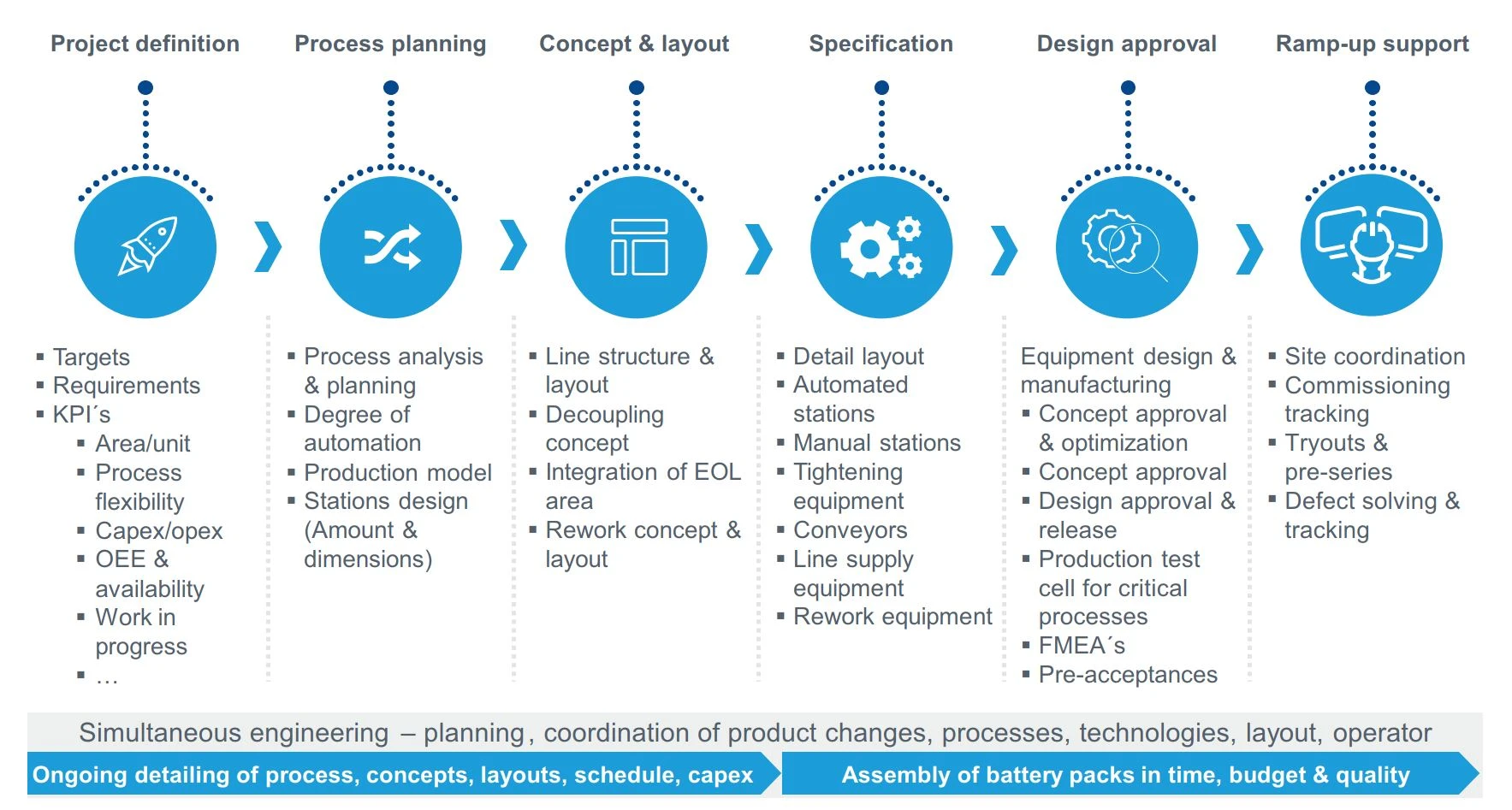
Wichtigste Herausforderungen des Projekts
Montagezeit: Zu Beginn des Projekts liegt der Schwerpunkt auf der Definition des Prozesses und des Inhalts der Automatisierung, um die erforderliche Montagezeit zu erreichen. Da die Massenproduktion von Batteriepacks für BEV eine relativ neue Anforderung für etablierte OEMs ist, müssen die spezifischen Standards, Technologien, Prozesse und Produktionszeiten überprüft und an die neuen Prozesse und Technologien angepasst werden. Daher war es sehr wichtig, einen realistischen Montageprozess und realistische Zeiten für die gesamte Montage und Prüfung einschließlich der Tests abzuschätzen und zu erstellen:
- Definition und Dimensionierung von Raum, Fluss, Stationsdesign und -anzahl, Entkopplung
- Entwicklung und Auswahl der benötigten Technologie, insbesondere für Hochspannung
- Bewertung und Festlegung des Automatisierungsgrades
Produktreife: Viele Änderungen am Produkt erzwingen einerseits eine laufende Überarbeitung der Prozesse, Technologien und Abläufe, ohne den Zeit- und Platzbedarf zu erhöhen. Andererseits bietet dies die Möglichkeit zur Integration von Produktmerkmalen (z.B. Referenzbohrungen), was eine Optimierung der Prozesse und eine höhere Fertigungsqualität ermöglicht.
Platzangebot: Die Herausforderung bestand darin, die Batteriepacks auf einer vorgegebenen Grundfläche unterzubringen. Um den Platz für die Montagelinien und -geräte zu maximieren, müssen notwendige Funktionen wie Übergaben von Linie zu Linie, Entkopplung und Pufferung, Schaltschränke, Reinigungsgeräte/-stationen, Wartungs- und Büroräume evaluiert und alternative Lösungen für die Raumoptimierung, z. B. Plattformen oder ein zweites Stockwerk, gefunden werden.
Weitere Herausforderungen
Darüber hinaus müssen die folgenden Herausforderungen durch die Optimierung und Entwicklung von Verfahren bewältigt werden:
- Hohe Verbindungsgenauigkeit bei der Montage von Modulen im Vergleich zu erreichbaren Toleranzen bei Batterieträgern und Produktionskosten
- Elektrische Vorschriften und neue Anforderungen für die Montage unter Hochspannung sollten nicht zu zusätzlichen Bearbeitungszeiten und Prüfungen führen oder die Gesamteffektivität einschränken
- Vorläufige Zulassungen nur bei Vorserienteilen, die nicht das endgültige Seriendesign haben
Erfolgsfaktoren und Highlights des Projekts
Die Zusammenarbeit mit Dürr Consulting ermöglicht es dem OEM-Kunden, eine hochmoderne Batteriepack-Baugruppe zu entwickeln, zu installieren und in Betrieb zu nehmen.
- Simultaneous Engineering und Design for Manufacturing in enger Zusammenarbeit mit Produktentwicklung, Produktionsplanung und Betriebsbereich
- Strenges Projekt- und Schnittstellenmanagement sichert die termingerechte und qualitativ hochwertige Realisierung innerhalb des Projektbudgets
- Zeitnahe Prozess-, Geräte- und Systemfreigaben durch strikte Maßnahmenverfolgung
- Hoher Teamgeist: hohes Engagement und Bereitschaft, die "Extrameile" zu gehen
- Benchmark-Konzept für künftige Batteriemontageprojekte
Ausblick: OEE-Optimierung durch digitale Anwendungen
Skalierbare und flexible Batteriebaugruppen mit steigenden Produktvarianten erfordern digitale Anwendungen, die die OEE verbessern und die Fertigungsprozesse stabilisieren. Dürr Consulting ist in der Lage, Beratung, Richtungsbestimmung und Implementierung von digitalen Lösungen für Batteriebaugruppen zu leisten. So sichern wir die Anlagenverfügbarkeit und gleichzeitig die Produktqualität. Unser Digital Readiness Assessment für den Shopfloor liefert innerhalb von 3 Tagen ein aktuelles Spiegelbild Ihrer Digital Readiness und ermöglicht die Diskussion von Maßnahmen zur weiteren Effizienzsteigerung in Ihrer Produktion.